THERMOPHOTOVOLTAIC ELECTRIC POWER GENERATION USING EXHAUST HEAT
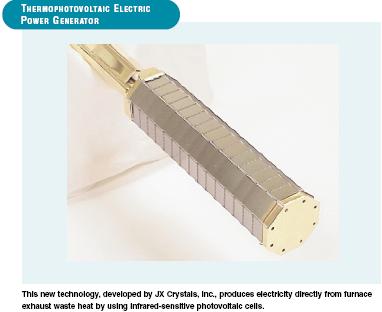
Furnaces in the glass, metalcasting, and steel industries operate at very high
temperatures and lose tremendous amounts of energy in their exhaust streams.
With the emissions-reducing shift to gas-oxy furnaces in these industries,
exhaust temperatures are climbing even higher. Waste heat from furnaces in
the glass, metalcasting, and steel industries is usually vented to the atmosphere.
In some facilities, it must be diluted with cool air to reduce its temperature prior
to venting. Until now, the venting of this waste heat has represented the loss of
a valuable resource.
A new technology adds value to this waste stream by using exhaust heat to
generate hundreds of kilowatts of electricity. This unique innovation uses new
infrared-sensitive photovoltaic cells mounted inside ceramic tubes. These tubes
are heated in the exhaust stream of an industrial process and radiate energy
inward to the photovoltaic cells to generate electricity directly from the waste
heat. The energy density in these systems is over 100 times that of solar energy,
producing over 100 times the energy of conventional photovoltaic or solar cells.
Economics and Commercial Potential
Exhaust heat offers an attractive energy alternative to the glass, metalcasting, and steel
industries. In particular, JX Crystals, Inc., has targeted the glass industry because of
an estimated 67 MW of year-round electrical generation available in this industry alone.
The technology has already attracted the partnership of a major glass-industry player
interested in demonstrating the technology on a glass furnace.
Given additional investment in the business and a market volume well over 10 MW per
year, JX Crystals, Inc., estimates the thermophotovoltaic circuit to cost approximately
$0.20 per watt. Balance of system costs are estimated to be $0.50 per watt. Assuming
a price of $1 per watt, utility rates of $0.05 per kWh, and a duty cycle of 90%, the
payback period should be less than 3 years.
This technology could save 27 billion Btu of electricity per installed unit each year. First
sales for the technology are expected by 2004. Based on 25% market penetration by
2010, annual savings could be 0.5 trillion Btu with 18 units installed, each containing 200
5-kW tubes. Market penetration of 50% by 2020 could save 1.0 trillion Btu from the
operation of 37 units by the glass industry.
0 Comments:
Post a Comment
Subscribe to Post Comments [Atom]
<< Home